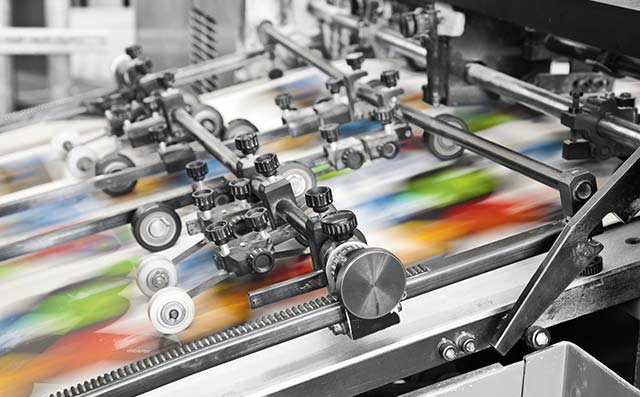
Why conduct Vibration Testing on Motors
Vibration monitoring is the industry standard for assessing if electric motors are at risk of failing. It has been proven that of all the types of non-destructive testing that can be conducted on a motor, vibration data gives the most insight about the motor’s condition. Similar to a doctor taking the vitals on a human to get a reading on the health of the patient, monitoring the vibration characteristics of a motor gives us data on the health of a motor. We can then use this data to take action before a problem becomes serious. If a problem goes undetected, a motor can eventually fail, causing businesses thousands of dollars to repair or replace parts. Even more harmful is the downtime created, reducing plant efficiency.
The most common reasons for vibration are
- Looseness
- Misalignment
- Imbalance
- Worn machine components
- Resonance
Vibration waves are usually described in terms of amplitude and frequency. Amplitude is the intensity of vibration, while frequency is the oscillation rate, or the number of cycles of oscillation in a second. The vibration data is collected with the help of a sensor called an accelerometer, which can sense the vibration of a motor in the three axes – axial, radial and tangential. The data can then be viewed in either a time domain view or a frequency spectrum.
However, for the purpose of analyzing motor health, the frequency spectrum view is far more helpful. The frequency spectrum is obtained with the help of a mathematical transformation called the Fast Fourier Transform (FFT). When graphed, the frequency spectrum data shows the frequencies at which the motor is vibrating along with the amplitudes of the vibrations. Analysts can now use this data to make an assessment on the health of the motor, as well as compare the frequency and amplitude data with the operating speed and make an assessment for likely causes of the unwanted vibration.