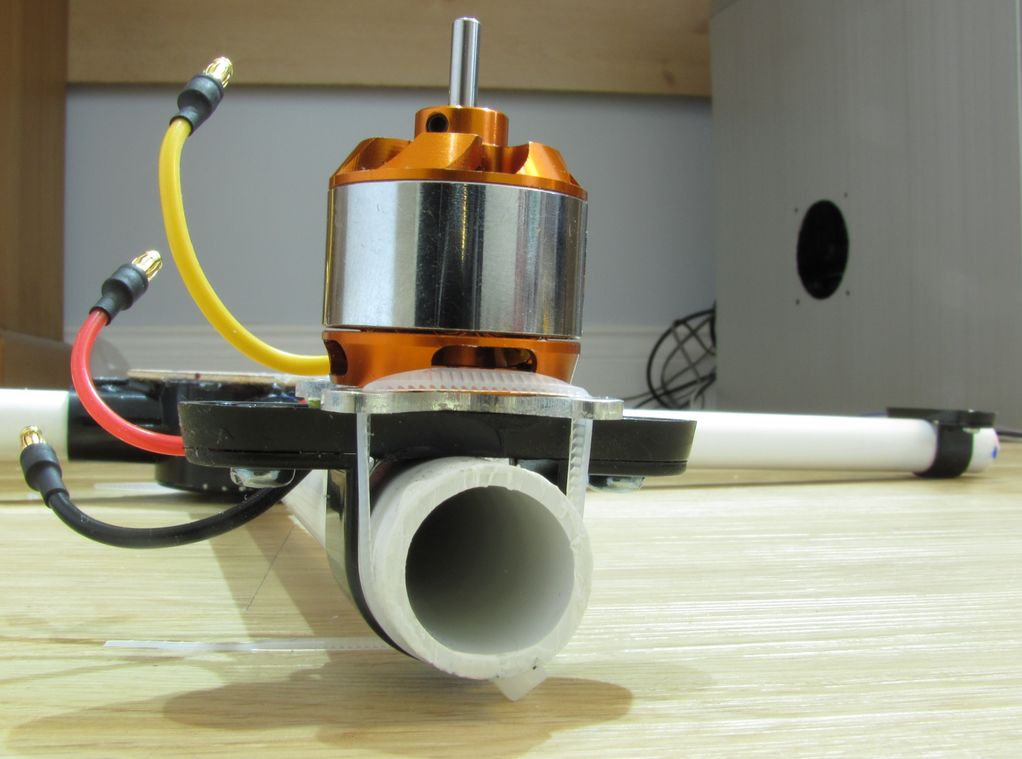
Despite the obvious benefits of vibration analysis there are significant obstacles to having a vibration program that can be widely deployed.
Even though it is well understood that a vibration monitoring program can help plants to fix motor problems before they occur, there are significant challenges to deploying a vibration program at the plant.
The most common vibration monitoring system in use now is the portable machine. An analyst will walk around with a portable machine, mount a sensor on a motor, and then take a reading in order to analyze the data. There is one downside to this method: the process is cumbersome, preventing plants from performing regular data collections. Plants are also straining to find resources to go around collecting the data. As a result, the time between readings may be too long, and the motor may fail in between readings. Because plant operators cannot see the status of their motors 24/7, they are often only aware of issues after the motor has spent a significant amount of time in a crippled state, or has failed entirely. Either way, repairs and/or replacements are costly.
Another issue is cost. Current vibration health systems in the marketplace are very expensive, preventing many small and medium sized plants from conducting vibration analysis. Even large plants have trouble monitoring all of their critical motors on a regular basis.
In order to address the issues above, a new system will be designed with the following four qualities:
- The system can be mounted on the motor to provide data 24/7
- The system provides the capability to monitor the data remotely
- The system is capable of sending alerts to notify the analyst of problems early
- The system must be inexpensive in order to be affordable for small, medium and large plants!